Chlor-alkali industry valve application
In a chlor-alkali plant, four main stages occur: brine preparation, chlorine handling, caustic soda and hydrogen production. Each of them presents its own challenges, as do other downstream considerations for chlor-alkali, including handling hydrochloric acid and sodium hypochlorite synthesis. Each of the four stages requires specific valves and materials.
The types of valves used in chlor-alkali plant are very wide: diaphragm valve, sleeve cock valve, lined valves (butterfly valve, ball valve, check valve and plug valve) and bellows sealed stop valves.
All of these valves face escape emission problems, which may be due to inadequate sealing systems, thermal cycling and wetting valve assembly corrosion, especially in the case of improper media / liner combinations. Downstream leakage is another common problem and may be due to internal corrosion, seat wear, and scaling. The valves used in chlor-alkali must have the characteristics and advantages that can solve these problems.
Challenges of valves in the manufacturing process
Saline preparations are plagued by corrosive and corrosive media. Wear occurs in the accumulation of solid particles and salts, and scaling may occur. The brine itself is a mixture of water and raw salt, which is highly corrosive and has a high ion concentration. Due to the high sensitivity of the membrane and septum in the electrolytic pool used in this process, saline solutions of these cells must be purified in a process that involves many steps including processing, filtration, and ion exchange. In the parts of the process, wear is a problem.perfluoroalkoxy (PFA) -lined diaphragm valve with polytetrafluoroethylene (PTFE) diaphragm is usually used. PFA lined butterfly valves are also a common choice in brine preparation, sometimes using PFA lined stopcock and ball valves, especially after removing solids from the medium.
Chlorine is the main product of the chlor-alkali plant. This chlorine must be cooled, dried, compressed, and liquefied for storage or transportation, or sent to a downstream process. The operating chlorine treatment section, after producing chlorine gas in the electrolytic cell. The most common problems encountered in chlorine treatment are escape emissions and corrosive media. Wet chlorine derived directly from the electrolytic cell is highly corrosive and toxic. The valves often selected here are high-performance butterfly valves, severe working condition plug valves for materials such as Monel, or zero discharge valves such as bellows seal stop valves. Use concentrated sulfuric acid (H2SO4) to dry the wet chlorine. Lined ball valves or stopcock are usually used to treat the high corrosion of H2SO4.
Another major byproduct of the chlor-alkali method is caustic sodium, usually sodium hydroxide. According to the technique used in the electrolytic cell, the concentration of salt pollution varies. This poses a challenge for valve selection because the medium is corrosive, but it may also contain solids, especially for concentrated products after evaporation. With increasing concentration, the salt may precipitate (sediment) from the solution and have a scaling effect. The sediment scale on the valve plate or sealing surface causes irreversible damage to the valve and affects the production efficiency. The rotating butterfly valve, hemisphere valve and plug valve shall have shear and scraping function to remove scaling and ensure the service life of the valve. The absence of a body cavity in this valve type prevents the accumulation of flow media, which may cause damage to the sealing surface. In low salt corrosive applications, lined ball valves are a viable option because of their full aperture design and excellent corrosion resistance.
Hydrogen gas is another by-product produced in the chlor-alkali process. Due to the unfavorable stoichiometry ratio (the exact ratio between the air being fully burned and the combustible gas or steam) and the low molecular weight, the amount of hydrogen produced does not make it a commercially attractive derivative. Nonetheless, the produced hydrogen can be burned as fuel or often with chlorine to prepare hydrochloric acid for factories. Difficulties in hydrogen production include the high pressure required for storage and the need to choose materials that can avoid hydrogen embrittlement. High-performance butterfly valve (HPBV) is a common choice for hydrogen production.
Hydrochloric acid
Typical valves: Diaphragm valve , lined ball, butterfly valve, check valve , plug valve , bellows sealed stop valve
Common problems solved: Downstream leakage , external emissions , internal corrosion , high maintenance costs
Brine preparation
Typical valves: Diaphragm valve lined plug valve, butterfly valve , ball valve , bellows sealed stop valve
Common Problem Solving: Particle Wear, Valve Blockage, Internal Corrosion , Scaling , Downstream Leakage
Chlorine Processing
Typical valves: Diaphragm lined butterfly valve, ball valve and plug valve bellows sealed stop valve for wet chlorine gas: lining
Common Problems Solved: External Discharge , Downstream Leakage, Liner Penetration, Maintenance Difficulties , Temperature Cycling
Caustic Soda
Typical valves: Stainless steel , lined butterfly valve , plug valve , sleeve plug valve
Common Problem Solving: External Leakage , Scaling , Downstream Leakage, High Temperature Corrosion
Chlor-alkali is one of the most demanding fluid handling applications. A better understanding of the challenges valves face in chlor-alkali production allows valve selectors to weigh the benefits and features of each valve type to meet their exact needs. It is up to operators to ensure they partner with a valve manufacturer that has the experience and knowledge needed to provide the most appropriate valves so that the equipment can both do the job it needs to run smoothly , while keeping people and the environment safe.
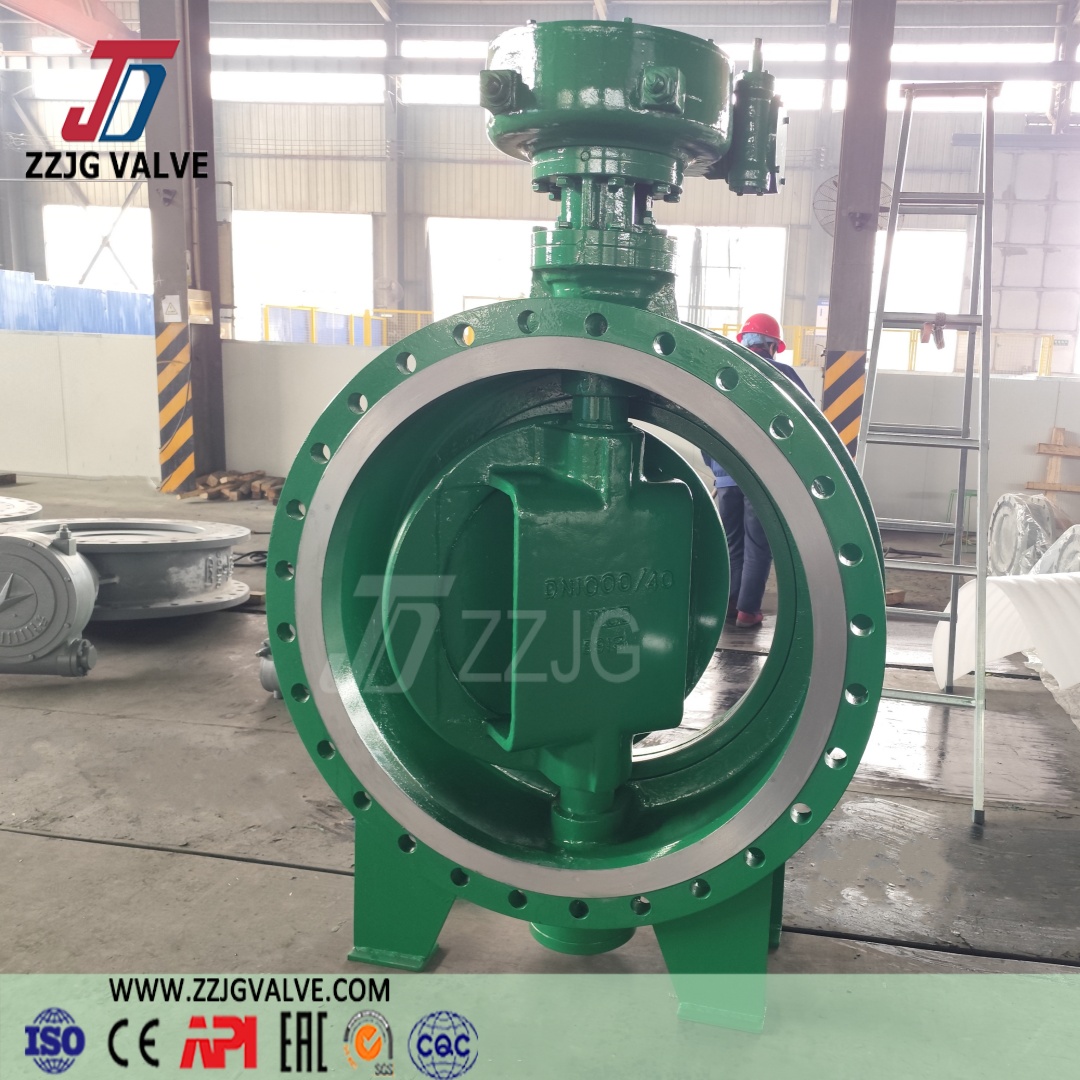
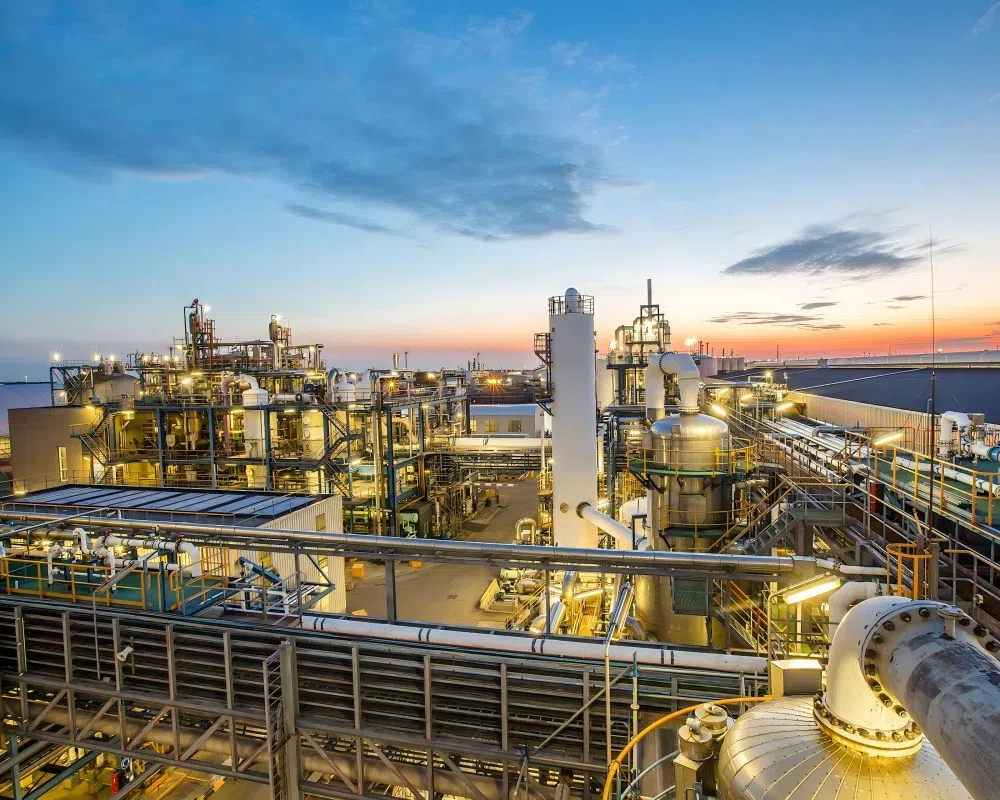
Next: ZZJG Ventilation Butterfly Valve